Oberflächentechnik
Optimale Verarbeitung
Oberflächentechnik
Die optimale Verarbeitung der einzelnen Werkstücke rundet CONDOR® Custom Solutions mit individuell angepassten Methoden der Oberflächenveredelung ab. Ob Gleitschleiftechnik, Mikrostrahltechnologie oder Oberflächenfinish – wir geben Ihren Werkstücken den letzten Schliff und bieten beständige, reproduzierbare Veredelungsqualität sowie Präzision auf Top-Niveau.
Gleitschleifen Trowalisieren
Durch das Trowalisieren bieten wir die Möglichkeit, Oberflächen von Werkstücken glätten, polieren oder aber schleifen zu lassen, ohne gefährliche Kanten.
Wir bieten innerhalb unserer Leistungen auch das Trowalisieren beziehungsweise Gleitschleifen an. Dieses Verfahren garantiert eine perfekte Kantenveredelung mittels unserer Gleitschleifanlage. Das kalkulierte Zusammenspiel von Wasser, Steinen (Schleifkörper) und einer Zusatzlösung garantiert exzellent abgerundete Kanten. Ebenfalls können Oberflächen geglättet und entzundert werden. Das sorgt für perfekte Ergebnisse, die sich insbesondere durch den Anspruch in Bezug auf die Optik auszeichnen.
Durch das Trowalisieren bieten wir die Möglichkeit, Oberflächen von Werkstücken glätten, polieren oder aber schleifen zu lassen, ohne gefährliche Kanten – dann sind sie bereit für den Einsatz oder aber die Oberflächenveredelung. Unser Leistungsspektrum beim Trowalisieren lässt sich je nach Werkstoff, Werkstück und Wirkungsgrad individuell anpassen: Speziell abgestimmt auf Ihre Bedürfnisse können wir die Schleifkörper sowie die wässrige Lösung abstimmen.
Der Vorgang
Beim Trowalisieren handelt es sich um ein Fertigungsverfahren, das zur Veränderung von Oberflächen seit knapp 80 Jahren angewendet wird. Die fertigen Werkstücke werden beim Trowalisieren zum Polieren oder Schleifen in unsere Gleitschleifmaschine gegeben. Dabei können auch mehrere Werkstücke gleichzeitig behandelt werden, denn hier geht es nicht um die Bearbeitung von Einzelteilen, sondern um die Behandlung der gesamten Oberfläche metallischer Produkte innerhalb des Behälters.
Zu den Werkstücken kommen dann die Schleifkörper als Schüttgut, eine wässrige Lösung sowie Wasser, sodass eine gleichmäßige Behandlung erfolgen kann. Dann rotiert oder oszilliert der Behälter und durch die Reibung werden die entsprechenden Ergebnisse erzielt.
Vorteile
- Problemloses Glätten, Schleifen oder Polieren
- Gefährliche Kanten und Ecken werden entfernt, die Oberfläche kann verdichtet werden
- Die Oberfläche kann je nach Bedarf behandelt werden, sodass sie Glanz oder Mattheit besitzt
- Fette sowie Öle werden beim Trowalisieren durch die Schleifkörper vollkommen entfernt, sodass ein sauberes Werkstück bleibt
Der Vorgang
Das Aluminium eloxieren beinhaltet innerhalb des Eloxal Verfahrens mehrere Schritte, die zu einer Schichtbildung durch Oxidation führen. In einer vereinfachten Form kann der Prozess so dargestellt werden: Zuerst werden die Werkstücke entfettet und gebeizt: Dabei wird es mit einer basischen, dann mit einer sauren Lösung behandelt. So wird die natürliche Oxidschicht entfernt sowie erste kleine Oberflächenfehler werden korrigiert. Die exakte Wahl der Chemikalien hängt stets von der Beschaffenheit des einzelnen Werkstoffes ab.
Im Anschluss erfolgt das eigentliche Aluminium eloxieren: Die erreichte poröse Schicht wird je nach Bedarf mit Farbstoffen gefärbt und im Anschluss mit heißem Wasser oder Dampf verdichtet. Teil beim Aluminium eloxieren ist die Elektrolyse, wobei mittels elektrischen Stroms eine weiche, mittelharte oder harte Schicht erzeugt wird, die vor Korrosion schützt, je nach individueller Anforderung.
Vorteile
- Verhinderung oder aber Minderung der Korrosion durch Oxidation
- Erreichung von Härten bis zu 200 und 350 HV
- Ungefärbte und gefärbte Oxidationsschichten möglich, beispielsweise für eine bessere Wärmeabstrahlung bei Kühlkörpern
- Dauerhafte Schutzschicht durch oxidative Veränderung der ersten Metallschicht
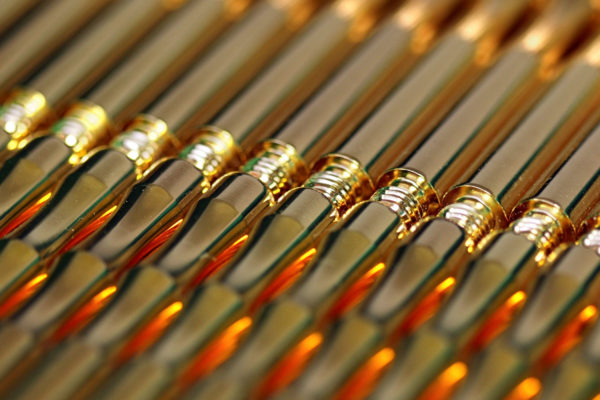
Aluminium Eloxieren
Wenn Aluminium im Rohzustand der Witterung oder Sauerstoff aufgesetzt ist, kommt es oft zu einer Korrosion. Dabei bildet sich eine optisch unschöne und auch funktional negative Oxidationsschicht, die die Langlebigkeit des Materials maßgeblich beeinflussen kann. Daher bieten wir Ihnen im Rahmen der Oberflächenbeschichtung das Verfahren „Aluminium eloxieren“ an, wodurch Sie die Qualität Ihrer Produkte konstant hochhalten und ein Mehr an Möglichkeiten erzielen können.
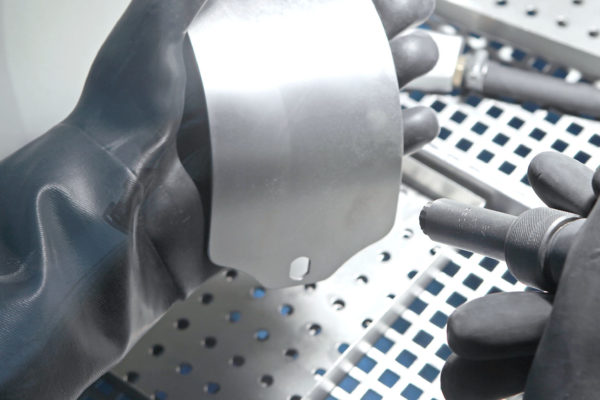
Perlstrahlen
Eine edle Mattierung realisieren wir mit der Mikrostrahltechnologie. Durch den Einsatz von Glasperlen mit einer Korngröße von 40 bis 70 µm sind wir imstande, die Beschaffenheit und Eigenheiten von Oberflächen zu verändern.
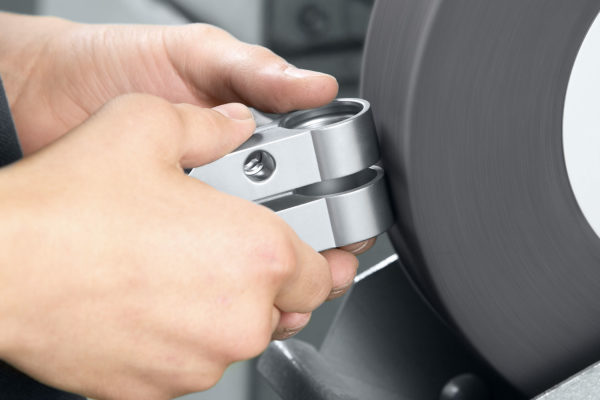
Oberflächenfinish
Flächen glatt und blank polieren und schleifen – bei der Endbearbeitung der Flächen setzt CONDOR® Custom Solutions alles daran, ein strahlendes Ergebnis zu präsentieren.